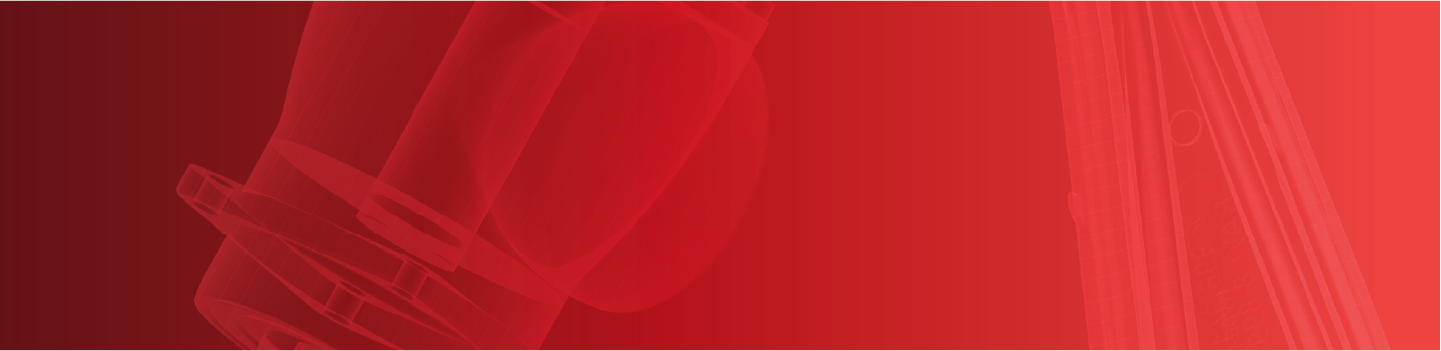
Röntgenprüfsysteme für Turbinenblätter
Die Qualitätssicherung von Turbinenschaufeln ist ein entscheidender Prozess in der Herstellung von Turbinen und anderen ähnlichen Anwendungen, die Schaufeln zur Energieumwandlung oder zum Antrieb nutzen. Turbinenschaufeln müssen höchsten Qualitätsstandards entsprechen. Die Qualitätssicherung umfasst verschiedene Schritte und Techniken, um sicherzustellen, dass die Schaufeln den erforderlichen Spezifikationen entsprechen, und erfordert die Zusammenarbeit verschiedener Fachleute, darunter Ingenieure, Inspektoren und Materialwissenschaftler. Durch diese umfassenden Kontrollen und Prüfungen können Hersteller sicherstellen, dass ihre Turbinenschaufeln sicher, zuverlässig und leistungsfähig sind.
Turbinenschaufeln können in Leitschaufeln (Statorschaufeln) und Laufradschaufeln (Rotorblätter) unterteilt werden. Leitschaufeln sind feststehende Schaufeln, die den Fluidstrom in der Turbine lenken, während Laufradschaufeln beweglich sind und auf der Turbinenwelle montiert werden. Es gibt verschiedene Arten von Turbinenschaufeln, die in Gasturbinen und Dampfturbinen verwendet werden, je nach den spezifischen Anforderungen der Anwendung. Axiale Schaufeln sind flach und dünn und entlang der Turbinenachse angeordnet, während radiale Schaufeln gekrümmt und radial zur Turbinenachse angeordnet sind. Moderne Turbinen können auch verstellbare Schaufeln haben, um sich an verschiedene Betriebsbedingungen anzupassen. Die Materialien und Fertigungstechniken von Turbinenschaufeln werden stetig weiterentwickelt, um eine höhere Leistung, Effizienz und Zuverlässigkeit zu gewährleisten. Abhängig vom Typ gibt es unterschiedliche Anforderungen an die Qualitätssicherung.
Die Herstellung von Turbinenschaufeln mittels Investment Casting, auch als "verlorene Form"-Gießverfahren bekannt, beinhaltet die Erstellung eines Wachsmodells, das an einem Gießbaum befestigt wird. Um das Modell wird eine Keramikschale aufgebaut. Das geschmolzene Metall wird in die Keramikform gegossen, wobei das Wachs schmilzt und Hohlräume bildet. Nach dem Abkühlen werden die Turbinenschaufeln entformt, nachbearbeitet und einer gründlichen Qualitätskontrolle unterzogen. Dieser Prozess ermöglicht die Produktion von Schaufeln mit präziser Geometrie und glatter Oberfläche, die den anspruchsvollen Anforderungen von Turbinenanwendungen gerecht werden. Bei diesem Fertigungsverfahren kann es zu einer Vielzahl von Defekten kommen, die mittels zerstörungsfreier Werkstoffprüfung getestet werden müssen.
Die Materialprüfung von Turbinenschaufeln bringt einige Herausforderungen mit sich bringen, aufgrund der spezifischen Anforderungen und Eigenschaften dieser kritischen Komponenten.
Um diesen Herausforderungen zu begegnen, sind hoch entwickelte Prüftechniken wie Röntgenprüfung entscheidend. Durch eine sorgfältige und umfassende Materialprüfung können Hersteller sicherstellen, dass ihre Turbinenschaufeln den strengen Anforderungen gerecht werden und eine sichere und zuverlässige Leistung gewährleisten.
Dieser Defekt tritt auf, wenn im gegossenen Material kleine Hohlräume oder Poren entstehen. Porosität kann die mechanischen Eigenschaften des Materials beeinträchtigen und in stark beanspruchten Bereichen zu Schwachstellen führen.
Wenn das flüssige Metall nicht vollständig alle Bereiche der Gussform erreicht, kann dies zu unvollständig ausgefüllten Schaufeln führen, was zu unregelmäßigen Formen oder Abweichungen von den Spezifikationen führen kann.
Einschlüsse sind Verunreinigungen oder Fremdkörper, die in das gegossene Material gelangen können. Sie können die Materialfestigkeit verringern und die Strömungseigenschaften der Schaufel beeinträchtigen.
Risse können entstehen, wenn es beim Gießprozess zu einer ungleichmäßigen Abkühlung kommt oder wenn das Material unter mechanischen Belastungen während des Gießens bricht.
Schwindung tritt auf, wenn das Material während des Abkühlens seine Form leicht verändert und Schrumpfungen auftreten. Dies kann zu Maßabweichungen oder Verformungen führen.
Wachsschmelzlöcher entstehen, wenn während des Ausschmelzens des Wachses nicht alle Hohlräume vollständig gefüllt werden, was zu Defekten in der Gussform führen kann.
Die Röntgenprüfung bietet für Materialprüfung von Turbinenschaufeln zahlreiche Vorteile. Es handelt sich um eine nichtdestruktive Prüfmethode, die verdeckte Defekte wie Risse, Lunker oder Einschlüsse erkennt und bietet eine hohe Genauigkeit bei der Detektion von Defekten. Sie kann auch sehr kleine Unregelmäßigkeiten oder Hohlräume identifizieren, die für die Leistung und Zuverlässigkeit der Turbinenschaufeln entscheidend sein können. Die Röntgenprüfung oder CT-Prüfung kann in kurzer Zeit durchgeführt werden, was zu einer effizienten Qualitätskontrolle und Produktionsprüfung führt. Dies ist besonders wichtig in der Massenproduktion von Turbinenschaufeln, um einen reibungslosen Fertigungsprozess zu gewährleisten.
Die Anforderungen von Herstellern an die Qualitätskontrolle sind sehr unterschiedlich und lassen sich grob in drei Kategorien einteilen:
Hersteller, die geringere Stückzahlen produzieren, benötigen manuelle Systeme für die Prüfung kleiner Chargen oder Einzelprüfungen. Hier ist die ECO H-Serie die perfekte Systemfamilie für kleinere Bauteile.
Hersteller von mittleren Volumen benötigen eine stärkere Automatisierung der 2D-Prüfung und müssen möglicherweise auch die Qualität neuer Gießverfahren regelmäßig mit Hilfe von Computertomographen überprüfen. In diesen Fällen können die ECO C- oder PRO C-Familien perfekt geeignet sein, wenn die Produktionsprüfung in 2D bei Bedarf durch 3D ergänzt werden kann.
Im Falle von extrem hohen Volumen, zum Beispiel in der Serienfertigung, sind hoch-performante Inlinesysteme mit automatischer Auswertung nötig. Mittels Roboterbeladung oder direkt in die Fertigungsstraße integriert, können so kürzeste Taktzeiten erreicht werden.
Die Auswahl des richtigen Systems kann komplex sein, und eine gute Entscheidung muss viele Parameter wie Größe, Geschwindigkeit, Kosten usw. abwägen. Kontaktieren Sie unsere Produktspezialisten für weitere Beratung
Kontaktieren Sie uns noch heute
Verbessern Sie die Qualität und Sicherheit Ihrer Bauteile mit unseren hochmodernen Röntgensystemen und CT-Systemen. Kontaktieren Sie uns noch heute, um mehr über unsere Lösungen für die Materialprüfung zu erfahren. Unser Team steht Ihnen jederzeit gerne zur Verfügung, um Ihre Fragen zu beantworten und eine maßgeschneiderte Lösung für Ihre Anforderungen zu entwickeln.
Kontaktieren Sie unsere Experten, um über Ihre Projekte und Herausforderungen zu sprechen
Mit unseren Servicezentren und Hubs weltweit,
unterstützen wir Ihre Mitarbeiter mit maximaler
Effizienz in dem von Ihnen vorgegebenen Zeitrahmen und
ohne Ihren Betrieb zu unterbrechen.
Egal wo Sie sind, wir sind immer in Ihrer Nähe.
Unser Wissen und unsere Erfahrung
maximieren die Gewinne Ihres Unternehmens.