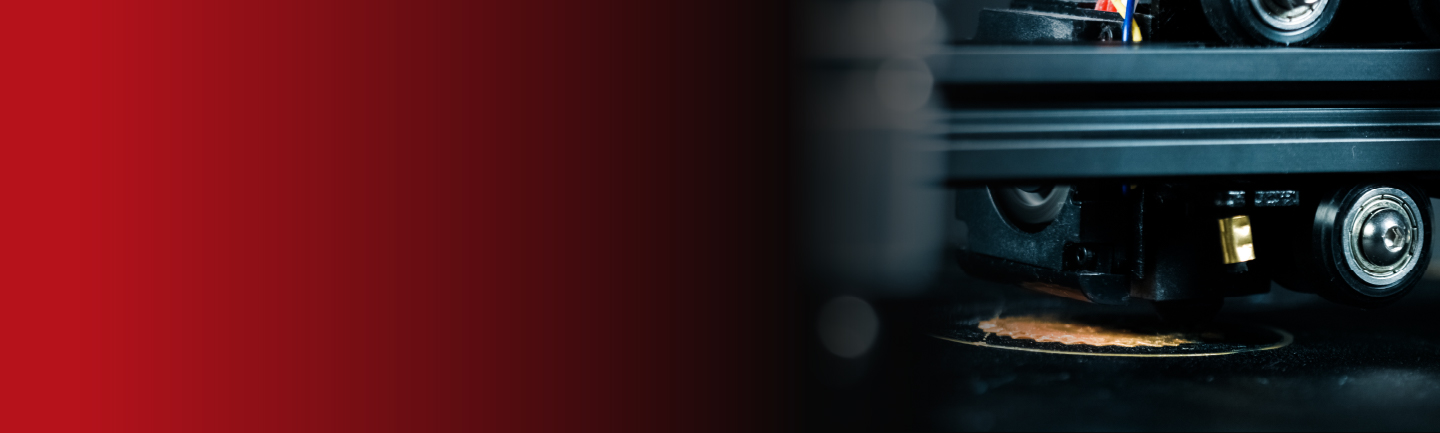
Making Additive Manufacturing perfect with CT testing
Additive manufacturing, also known as 3D printing, has sparked a revolution in industrial production in recent years. The ability to build complex components layer by layer has expanded design capabilities while shortening product development cycles. But the unique manufacturing processes and materials also pose new quality assurance challenges. Incomplete layers, pores, cracks and other internal defects can significantly affect mechanical properties and component life.
Additive manufacturing uses material deposited layer by layer to create a three-dimensional object. This process makes it possible to create complex structures that would be difficult or impossible to achieve using traditional manufacturing methods. Traditionally, subtractive was used, i.e. by means of material removal by a milling machine, for example. Due to the new process, quality assurance in additive manufacturing requires special attention, as the material properties and structure of the manufactured parts may be different from those of conventionally manufactured products.
Material testing of 3D printed additively manufactured components presents several challenges due to the specific manufacturing processes and material properties. Some of the main issues and challenges are:
To overcome these challenges, advanced inspection technologies such as computed tomography (CT) and specialized X-ray systems optimized for additive manufacturing are particularly important. These technologies enable comprehensive and non-destructive analysis of internal structures and defects in additively manufactured components to ensure high product quality and reliability. In addition, close cooperation between manufacturers, research institutions and testing experts is necessary to continuously improve material testing in additive manufacturing and to meet the growing requirements.
Pores are small voids or air bubbles inside the component. They can be caused by incomplete melting of the material, gas evolution, or insufficient compaction of the layers.
Voids are larger, irregularly shaped cavities in the component that may result from incomplete fusion of the material layers or uneven material flow.
Cracks can occur during the printing process, especially if rapid cooling and shrinkage of the material occurs
Overhangs are areas where the material is printed without support and hangs down due to gravity. This can lead to warping or deformation.
Warping occurs when the part warps or deforms during the cooling process. This can occur due to stresses in the material or uneven cooling. Warping leads to geometry deviations and possibly stress cracks.
Uneven or fuzzy edges can result from inaccurate print nozzle movement or poorly calibrated print parameters. Surface defects can also be caused by uneven material feed or layer adhesion.
If layers are not fused or deposited correctly, parts of the part may be missing or the density of the layers may vary.
Impurities or contaminants in the starting material can affect material performance and integrity.
Layer separation refers to the detachment of layers from each other or from the print bed, while delamination describes the detachment of material layers inside the component.
Errors in material supply can lead to over- or under-extrusion, which affects the dimensional accuracy and strength of the part.
Computed tomography (CT) offers a variety of benefits when inspecting additively manufactured parts using 3D printing. This advanced non-destructive testing method uses X-rays to create a 3D representation of a component's internal structures. This can effectively overcome many challenges encountered in the inspection of additively manufactured components.
Implementing CT inspection for 3D printed components requires specialized equipment and expertise. First, an appropriate inspection system must be selected that is suitable for inspecting 3D-printed components. This device should have the required resolution, beam energy and other features to achieve the desired results. Here, VCxray's application service is recommended to perform a feasibility study at an early stage. In doing so, we assess the feasibility for your component free of charge.
It is important to note that CT inspection is an advanced NDT process that may require specialized equipment, trained personnel, and in most cases, compliance with certain safety guidelines. Please do not hesitate to contact our specialists for a consultation.
Particularly in the case of lower production volumes and a high number of variants, it may not be worthwhile to purchase your own testing equipment. In this case, the testing service is a good solution. All you have to do is send the component and the inspection instructions to our laboratory. Our X-ray experts will then take care of recording the scan, evaluating the results and explaining them to you in detail.
VCxray offers the solutions
For many years, well-known companies in the additive manufacturing industry have relied on our high-precision X-ray systems and computed tomography solutions. Our technology has already helped ensure the quality and reliability of additively manufactured components in numerous projects.
Contact us today to learn more about our innovative material inspection solutions for additive manufacturing. Our dedicated team is available to help you successfully meet the challenges of your industry.
With our Service centers and Hubs worldwide,
we will complete your staff with maximum
efficiency in your specified time frame and
without interrupting your operations.
No matter where you are, we are never far away.
Our knowledge and experience
maximize your company‘s profits.