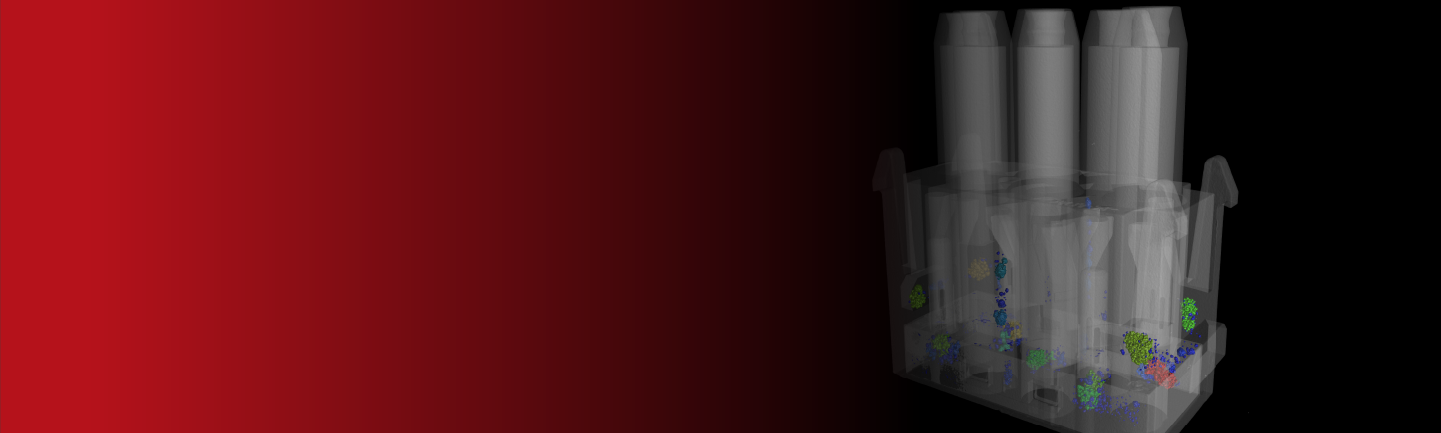
X-ray inspection systems for plastics
Quality assurance of plastic components is critical to ensure that the parts produced meet the required standards. This includes checking material quality, controlling production processes, dimensional and surface inspections, and strength and load tests. Spot checks and series tests help to identify potential problems at an early stage. Accurate documentation of all measures is important for traceability and problem analysis. Quality assurance aims to satisfy customers, minimize rejects and ensure product safety.
There are various processes for manufacturing plastic parts, including injection molding, extrusion, blow molding, thermoforming, rotational molding, compression molding and injection blow molding. Recently, plastic parts are also often manufactured additively using 3D printing. Each process has specific applications and benefits that are considered based on product complexity, quantity, material selection and cost. Choosing the right process depends on individual requirements and circumstances.
Materials testing of plastics presents some challenges due to their diverse properties and applications.
To overcome these challenges, it is important to use qualified professionals and specialized testing facilities that specialize in materials testing of plastics. A comprehensive knowledge of plastics properties and applications is critical to selecting effective test methods and obtaining accurate results. In addition, continuous development of test methods and standards is necessary to meet the changing needs of the plastics industry.
Air pockets or blowholes occur when air is trapped in the plastic during injection molding or other processes. This can result in voids or porous areas in the finished part.
Incomplete filling of the mold can result in incomplete parts, voids or uneven thickness.
Injecting too much plastic into the mold can result in excess material at the edges or undesirable molding.
Warpage occurs when the plastic part deviates from its desired shape after cooling. This can be caused by uneven shrinkage or uneven cooling.
Plastics tend to contract during the cooling process, which can lead to dimensional deviations.
Foreign bodies such as dirt, dust or other contaminants can get into the plastic part and cause visible defects.
Scratches, dents, efflorescence, or fuzzy edges can affect surface quality.
If the precision of the mold or the production process is not adequately controlled, dimensional deviations may occur.
The use of CT (computed tomography) metrology for plastic parts offers numerous advantages and is an extremely effective method for quality assurance and defect analysis. Thanks to high-precision 3D visualization, complex shapes, internal voids, and inclusions can be examined in detail. Since it is a non-destructive testing (NDT) method, the integrity of the parts remains unaffected. CT enables accurate detection of flaws and defects, helps analyze material density and homogeneity, and enables precise dimensional inspection. It also supports root cause analysis and promotes efficiency in production control. In research and development of new plastic parts, CT is a valuable tool for detailed analysis of prototypes and early detection of design flaws. Overall, the use of CT metrology enables comprehensive and reliable analysis of plastic parts, which helps improve product quality and process optimization and increases customer satisfaction.
The quality control requirements of manufacturers of plastic parts vary widely and can be roughly divided into three categories:
Manufacturers producing lower volumes require manual systems for small batches or single inspections. Small benchtop devices are often used in the laboratory.
Medium-volume manufacturers require more automated testing. Automated part changers or robotic loading from a pallet are ideal for this purpose. In the case of extremely high volumes, for example in series production in the automotive sector, high-performance inline systems with automatic evaluation are required. Through robot loading or directly integrated into the production line, the shortest cycle times can be achieved.
Of particular importance is the use of computer tomography systems in materials laboratories of plastics manufacturers. These devices can be used to perform demanding measurement tasks and material analyses. The data generated can be used to correct molds and optimize production parameters. In this context, it is important to ensure that the CT system is highly precise and capable of measuring.
Selecting the right system can be complex, and a good decision must weigh many parameters such as size, speed, cost, etc. Contact our product specialists for more advice.
Contact us today
Improve the quality and safety of your plastic components with our state-of-the-art X-ray systems and CT systems. Contact us today to learn more about our material inspection solutions. Our team is always available to answer your questions and develop a customized solution for your needs.
Contact our experts to talk about your projects and challenges
With our Service centers and Hubs worldwide,
we will complete your staff with maximum
efficiency in your specified time frame and
without interrupting your operations.
No matter where you are, we are never far away.
Our knowledge and experience
maximize your company‘s profits.