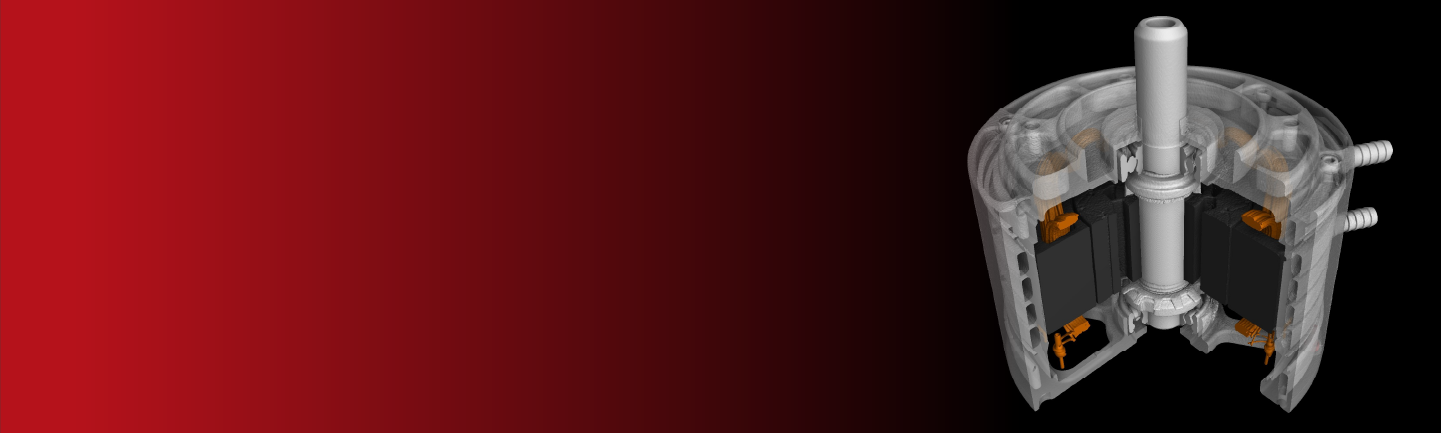
X-ray inspection systems for manufacturing
The purpose of quality assurance in manufacturing is to ensure that products or services meet established quality standards during production. This is done through quality management processes, careful planning, quality control, defect prevention, supplier management, documentation and continuous improvement. This holistic approach increases competitiveness and customer confidence, leading to long-term business success. Non-destructive material testing is an important aspect of quality assurance.
Various manufacturing processes are used in the manufacturing sector, including casting, forming, machining, joining, injection molding, assembly, extrusion, cutting, surface treatment and 3D printing. Selecting the appropriate process depends on the materials, design requirements, and economic aspects to efficiently produce high-quality products. Each of these processes has its own quality assurance and material testing challenges.
Materials testing in manufacturing faces several challenges that must be overcome to ensure the quality and reliability of manufactured products.
Cracks and fractures can indicate material weaknesses or stresses in the material that occurred during the manufacturing process or due to stress.
Porosity shows up as small holes, bubbles or voids in the material and can indicate inadequate melting or casting processes, especially in metallic materials.
Irregular structures such as grain size differences or inclusions may indicate problems in material processing or alloy composition.
A material sample may have lower strength than expected, which may indicate material defects or insufficient process parameters.
The hardness of a workpiece may be below required specifications, which may be due to inadequate heat treatment or material selection.
Deviations from the desired shape or dimension may indicate manufacturing errors or improper handling during shipping.
Materials may exhibit inhomogeneous properties that may be due to mixing problems or inconsistent heat treatment.
Wear or signs of fatigue may indicate material fatigue or insufficient strength, especially in components subjected to high loads.
Corrosion or rusting may indicate inadequate protective coating or improper material selection.
X-ray inspection is a non-destructive testing technique commonly used in manufacturing to check the quality of materials and products. It uses X-rays to make internal structures and defects in materials visible without damaging the material itself.
The selection of the appropriate method depends on the type of material, the size and nature of the object being inspected, and the specific inspection requirements. Overall, X-ray inspection is a valuable method for ensuring the quality and reliability of materials and products in the manufacturing industry. It is advisable to seek advice from a specialist company to select the appropriate system.
The quality control requirements of manufacturers in the manufacturing sector vary widely and can be broadly divided into three categories:
Manufacturers producing lower volumes require manual systems for small batches or single inspections. Small benchtops or mobile systems are often used in the laboratory.
Medium-volume manufacturers require more automated testing. Automated part changers, CNC systems, or robotic loading from a pallet can be used for this purpose. In the case of extremely high volumes, for example in series production in the automotive sector, high-performance inline systems with automatic evaluation are required. Through robot loading or directly integrated into the production line, the shortest cycle times can be achieved.
Choosing the right system can be complex, and a good decision must weigh many parameters such as size, speed, cost, etc. Contact our product specialists for further advice.
Contact us today
Improve the quality and safety of your components with our state-of-the-art X-ray systems and CT systems. Contact us today to learn more about our material inspection solutions for the manufacturing industry. Our team is always available to answer your questions and develop a customized solution for your needs.
Contact our experts to talk about your projects and challenges
With our Service centers and Hubs worldwide,
we will complete your staff with maximum
efficiency in your specified time frame and
without interrupting your operations.
No matter where you are, we are never far away.
Our knowledge and experience
maximize your company‘s profits.