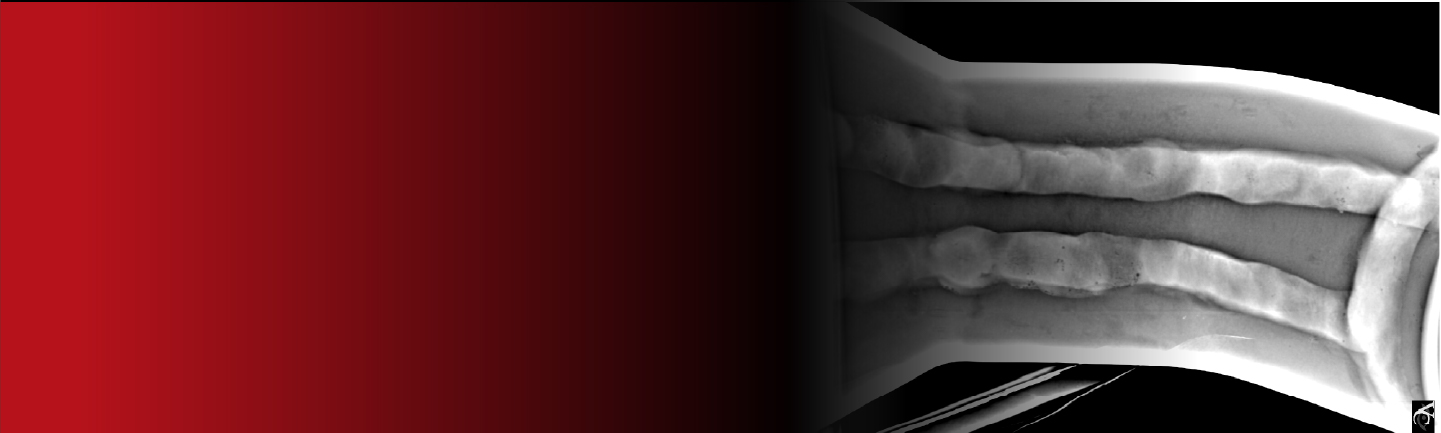
X-ray inspection of weld seams
X-ray inspection is a non-destructive testing method that is frequently used for material testing of weld seams. X-rays or gamma rays are sent through the weld and detected on the other side by a detector. Different thicknesses or densities in the material result in visible differences in the X-ray images. This allows weld defects such as incomplete penetration, pores, cracks, and material contamination to be detected. X-ray inspection is particularly important in safety-critical applications to ensure the quality and integrity of welded joints.
There are various welding processes such as manual arc welding (MMA), metal inert gas welding (MIG/MAG), tungsten inert gas welding (TIG), submerged arc welding (SAW), electron beam welding (EBW), and laser welding. Each process has specific applications, advantages, and disadvantages. The right choice of welding process depends on the materials, requirements, and desired quality of the welded joints. Accordingly, the requirements for material testing are also very diverse.
In non-destructive testing (NDT) of welds, certain requirements must be met in order to perform a reliable and meaningful inspection. Here are some of the important requirements:
Compliance with these requirements is critical to perform successful and meaningful nondestructive testing of welds and to detect potential defects or irregularities at an early stage.
If the weld does not penetrate deep enough into the base material, this can result in an inadequate joint and lower strength.
Gas bubbles trapped in the weld metal are called pores. They can weaken the weld and affect the sealing ability.
Voids are cavities or holes in the weld metal that can result from insufficient fusion of weld material.
If slag that forms during welding is not completely removed or trapped by the weld pool, it can lead to slag inclusions that weaken the weld joint.
Cracks can form either in the weld or in the heat affected zone and can affect the integrity of the weld joint.
During welding, materials can warp due to thermal expansion, which can lead to deformation or distortion.
If the weld metal is not sufficiently fused to the base material, this can result in a weak joint.
insufficient or excessive heat input can negatively affect the mechanical properties of the material.
Identifying and avoiding these defects is critical to ensure high quality and reliable welded joints. This is achieved through careful preparation, precise welding techniques and proper quality assurance. Non-destructive testing (NDT) such as X-ray inspection, are needed to detect and correct potential defects at an early stage.
X-ray testing is a non-destructive testing method that is commonly used for material testing of welds. X-rays or gamma rays are sent through the weld and detected by a detector on the other side. Different thicknesses or densities in the material result in visible differences in the X-ray images.
Internal defects such as pores, cracks, and incomplete penetrations can be detected. The method is fast, sensitive, and can be used on a variety of materials. The X-ray images show detailed structures, allow good documentation, and offer high safety standards. Because of these advantages, it is widely used in safety-critical industries such as aerospace, oil and gas, chemical, and pressure vessel construction to ensure the quality of welds.
International standards for the inspection of welds using X-rays include ISO 17636, API 5L, EN 1435, AWS D1.1, and ASME BPVC Section V. They define procedures and quality levels for non-destructive testing to ensure reliable and standardized inspection of welds. The selection of the appropriate standard depends on the specific requirements and applications.
Furthermore, there are industry-specific standards (e.g. NADCAP in the aerospace sector) and company-specific regulations that must be observed. In addition, image format requirements are often specified. For example, the internationally recognized DICONDE format is often required.
These standards ensure compliance with industry guidelines and ensure reliable and safe piping in various applications. Due to the high demands placed on testing technology in this highly sensitive area, it is strongly recommended that an expert consultant be consulted.
Automatic defect detection of X-ray images of welds is an area of machine vision that uses advanced technologies such as artificial intelligence (AI) and machine learning to automatically detect and classify defects in welds.
It speeds up the inspection process, increases the precision of defect detection, ensures standardized evaluation, enables classification and prioritization of defects, provides valuable insights through data analytics, and leads to cost savings through labor cost reduction and increased productivity.
However, it is important to note that automated defect detection is not a replacement for human inspectors but should be viewed as a supporting technology. Human expertise remains important to evaluate complex defects that may require specialized expertise. However, combining automatic defect detection with human inspection can be a powerful and efficient way to improve weld quality assurance.
Find out more about the potential of our ADR solutions for your application.
VCxray offers a variety of solutions for weld inspection.
For in-service testing, companies need portable systems that can be used to test for corrosion or wear in the field.
Testing at the end of the manufacturing process is of particular importance. Here, our customers can choose from an extensive portfolio of manual, semi-automatic, and fully automatic systems. Depending on how demanding the required cycle time is, the system is designed. Furthermore, there are specific solutions for clad pipes, spiral welded pipes, longitudinal welded pipes, and the screening of weld ends.
Choosing the right system can be complex, and a good decision must weigh many parameters such as size, speed, cost, etc. Contact our product specialists for further advice.
Can you imagine a digital decision-making assistant that supports you in making better decisions faster? Discover VCxray's AI-supported X-ray Copilot called COMPASS!
Contact us today
Improve the quality and safety of your welds and components with our state-of-the-art X-ray systems and CT systems. Contact us today to learn more about our material inspection solutions. Our team is always available to answer your questions and develop a customized solution for your needs.
Contact our experts to talk about your projects and challenges
With our Service centers and Hubs worldwide,
we will complete your staff with maximum
efficiency in your specified time frame and
without interrupting your operations.
No matter where you are, we are never far away.
Our knowledge and experience
maximize your company‘s profits.