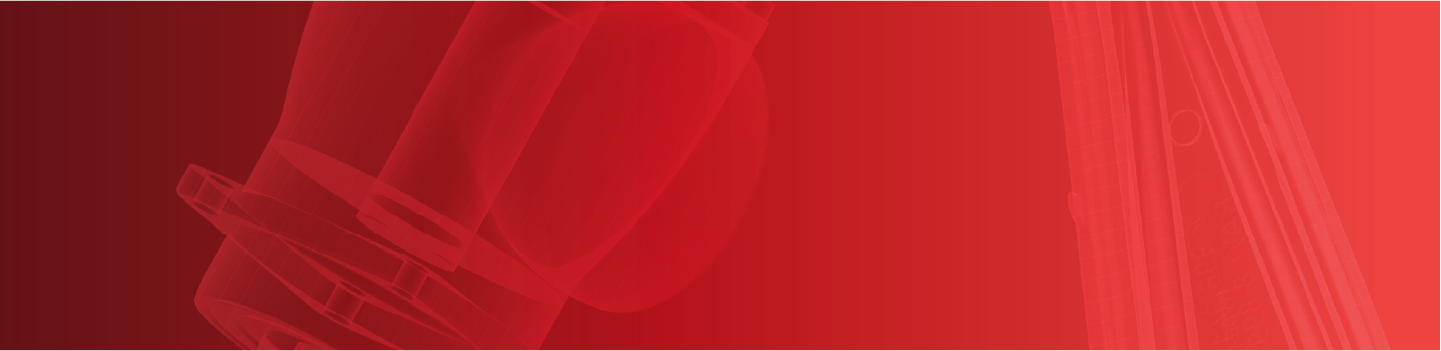
X-ray inspection systems for turbine blades
Turbine blade quality assurance is a critical process in the manufacture of turbines and other similar applications that use blades for energy conversion or propulsion. Turbine blades must meet the highest quality standards. Quality assurance involves various steps and techniques to ensure that blades meet required specifications and requires the cooperation of various professionals, including engineers, inspectors and material scientists. Through these comprehensive inspections and tests, manufacturers can ensure that their turbine blades are safe, reliable and efficient.
Turbine blades can be divided into guide vanes (stator blades) and runner blades (rotor blades). Stator blades are fixed blades that direct the flow of fluid in the turbine, while runner blades are movable and mounted on the turbine shaft. There are several types of turbine blades used in gas turbines and steam turbines, depending on the specific requirements of the application. Axial blades are flat and thin and arranged along the turbine axis, while radial blades are curved and arranged radially to the turbine axis. Modern turbines can also have adjustable blades to adapt to different operating conditions. Turbine blade materials and manufacturing techniques are constantly evolving to ensure higher performance, efficiency and reliability. Depending on the type, there are different quality assurance requirements.
The production of turbine blades by investment casting, also known as "lost mold" casting, involves the creation of a wax model that is attached to a casting tree. A ceramic shell is built around the model. Molten metal is poured into the ceramic mold, causing the wax to melt and form cavities. After cooling, the turbine blades are demolded, reworked and subjected to thorough quality control. This process enables the production of blades with precise geometry and smooth surfaces that meet the demanding requirements of turbine applications. This manufacturing process can result in a variety of defects that must be tested using non-destructive materials testing.
Materials testing of turbine blades presents several challenges due to the specific requirements and properties of these critical components.
To meet these challenges, sophisticated testing techniques such as X-ray inspection are critical. Through thorough and comprehensive material testing, manufacturers can ensure that their turbine blades meet stringent requirements and ensure safe and reliable performance.
This defect occurs when small voids or pores are created in the cast material. Porosity can affect the mechanical properties of the material and cause weak spots in heavily stressed areas.
If the molten metal does not completely reach all areas of the mold, this can result in incompletely filled blades, leading to irregular shapes or deviations from specifications.
Inclusions are impurities or foreign bodies that can get into the cast material. They can reduce material strength and affect the flow characteristics of the blade.
Cracks can occur when uneven cooling occurs during the casting process or when the material breaks under mechanical stresses during casting.
Shrinkage occurs when the material changes shape slightly during cooling and shrinkage occurs. This can lead to dimensional deviations or deformations.
Wax melting holes occur when not all cavities are completely filled during the melting out of the wax, which can lead to defects in the mold.
X-ray inspection offers numerous advantages for materials testing of turbine blades. It is a non-destructive testing method that detects hidden defects such as cracks, voids, or inclusions and provides high accuracy in detecting defects. It can also identify very small irregularities or voids that can be critical to turbine blade performance and reliability. X-ray inspection or CT inspection can be performed in a short time, resulting in efficient quality control and production inspection. This is especially important in the mass production of turbine blades to ensure a smooth manufacturing process.
Manufacturers' quality control requirements vary widely and can be broadly divided into three categories:
Manufacturers producing lower volumes require manual systems for small batches or single inspections. Here, the ECO H-Series is the perfect system family for smaller components.
Medium-volume manufacturers need more automation for 2D inspection and may also need to regularly check the quality of new casting processes using computer tomography. In these cases, the ECO C. or PRO C families may be perfectly suited if 2D production inspection can be supplemented with 3D as needed.
In the case of extremely high volumes, for example in series production, high-performance inline systems with automatic evaluation are required. Using robot loading or integrated directly into the production line, the shortest cycle times can be achieved.
Selecting the right system can be complex, and a good decision must weigh many parameters such as size, speed, cost, etc. Contact our product specialists for further advice.
Contact us today
Improve the quality and safety of your components with our state-of-the-art X-ray systems and CT systems. Contact us today to learn more about our material inspection solutions. Our team is always available to answer your questions and develop a customized solution for your needs.
Contact our experts to talk about your projects and challenges
With our Service centers and Hubs worldwide,
we will complete your staff with maximum
efficiency in your specified time frame and
without interrupting your operations.
No matter where you are, we are never far away.
Our knowledge and experience
maximize your company‘s profits.