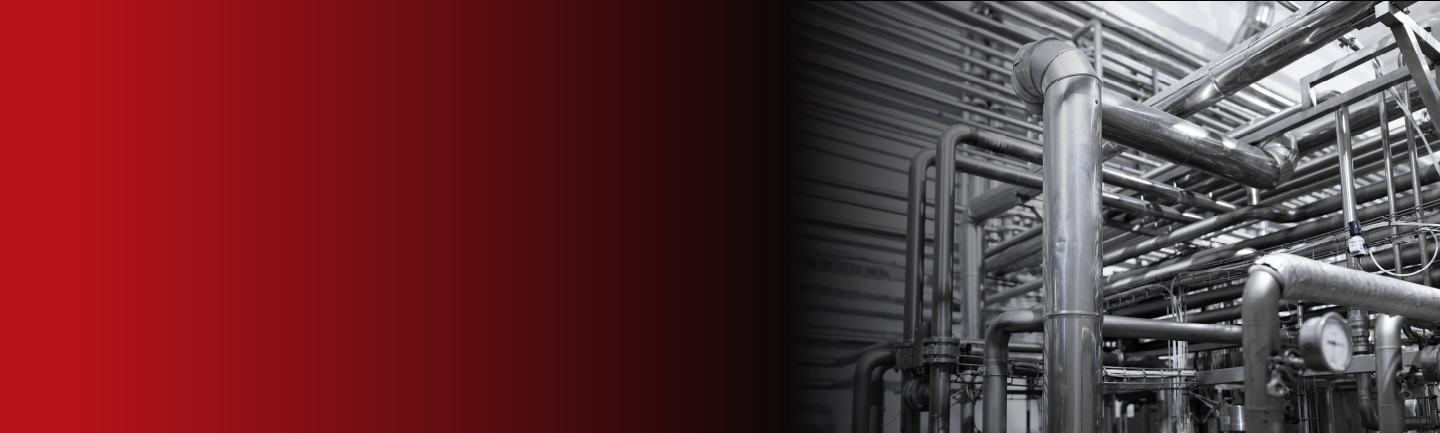
Röntgenprüfsysteme in der Öl- und Gasindustrie
Die Öl- und Gasbranche ist von großer Bedeutung für die moderne Weltwirtschaft. Sie versorgt uns mit Energie für Strom, Heizung und Transport und hat einen erheblichen Einfluss auf die globale Wirtschaft. Die Branche fördert Forschung und Technologie, erfordert jedoch eine umfangreiche Infrastruktur und hat potentiell negative Umweltauswirkungen. Angesichts der Energiewende suchen viele Anbieter Optimierungspotential in bestehenden Anlagen und dem Einsatz von erneuerbaren Energien, um die Abhängigkeit von fossilen Brennstoffen zu verringern. Dennoch werden fossile Brennstoffe in den nächsten Jahrzenten immer noch eine sehr große Rolle spielen. Daher gilt es den Betrieb der Infrastruktur maximal sicher zu betreiben.
Die Werkstoffprüfung in der Öl- und Gasindustrie ist von entscheidender Bedeutung, um Sicherheit, Zuverlässigkeit und Umweltverträglichkeit der Anlagen sicherzustellen. Sie gewährleistet, dass die verwendeten Materialien den extremen Bedingungen standhalten und korrosionsbeständig sind. Durch die Prüfung werden die Einhaltung von Vorschriften und Normen sowie die Entwicklung innovativer Materialien vorangetrieben. Dadurch werden Unfälle, Leckagen und Umweltverschmutzungen vermieden und die Effizienz der Industrie verbessert.
Der Einsatz von Röntgentechnik und Computertomographie (CT) spielt in der Öl- und Gasindustrie eine wichtige Rolle bei der Materialprüfung. Diese zerstörungsfreien Prüfmethoden ermöglichen eine detaillierte Untersuchung von Materialien und Komponenten, ohne sie zu beschädigen. Hier sind einige Bereiche, in denen Röntgentechnik und CT in der Branche eingesetzt werden:
Insgesamt tragen Röntgentechnik und CT zur Verbesserung der Materialprüfung und Qualitätskontrolle in der Öl- und Gasindustrie bei, was zu sichereren und zuverlässigeren Anlagen führt und letztendlich die Effizienz und Leistungsfähigkeit der Branche steigert.
Die Prüfgeräte für die Materialprüfung in der Öl- und Gasindustrie stehen vor verschiedenen Herausforderungen. Sie müssen robust und langlebig sein, um den extremen Umgebungsbedingungen standzuhalten. Zudem müssen sie mobil und leicht transportierbar sein, um vor Ort eingesetzt zu werden. Die Prüfgeräte müssen zerstörungsfreie Prüfungen ermöglichen, vielseitig einsetzbar, genau und zuverlässig sein. Die Einhaltung von Normen und Vorschriften, Schulung der Bediener und effizientes Datenmanagement sind weitere wichtige Aspekte. Die Bewältigung dieser Herausforderungen erfordert eine enge Zusammenarbeit zwischen Herstellern, der Industrie und Forschungseinrichtungen.
Die Ergebnisse der Materialprüfung sind von entscheidender Bedeutung für die Sicherheit und Integrität der Anlagen. Die Prüfgeräte müssen daher eine hohe Genauigkeit und Zuverlässigkeit aufweisen, um verlässliche Daten zu liefern. Außerdem unterliegt die Öl- und Gasindustrie strengen Standards und Normen in Bezug auf Sicherheit und Qualität. Die Prüfgeräte müssen diesen Vorgaben entsprechen und in der Lage sein, die geforderten Standards einzuhalten. Die Mitarbeiter, die die Prüfgeräte verwenden, müssen entsprechend geschult sein. Die Bedienbarkeit der Geräte sollte daher benutzerfreundlich und einfach sein, um sicherzustellen, dass die Prüfungen korrekt und effizient durchgeführt werden können. Ein extrem wichtiger Aspekt ist, dass die Prüfgeräte in der Lage sein müssen, die erfassten Daten effizient zu verwalten und zu dokumentieren. Dies ist wichtig, um die Ergebnisse zu archivieren, nachvollziehbar zu machen und für spätere Analysen und Entscheidungen zugänglich zu machen.
Internationale Standards zur Röntgenprüfung von Rohrleitungen sind unter anderem ISO 17636 für die Prüfung von Schweißnähten, und EN 10246-7 für die zerstörungsfreie Prüfung von Stahlrohren. Diese Standards legen Anforderungen und Verfahren fest, um eine zuverlässige und sichere Röntgenprüfung zu gewährleisten. Die Wahl des geeigneten Standards hängt von den spezifischen Anforderungen und der Anwendung ab.
API hat Standards für die Röntgenprüfung von Rohrleitungen entwickelt, einschließlich API 1104 für das Schweißen, API 5L für Rohrleitungen, API 5CT für Casing und Tubing sowie API 570 für In-Service-Inspektionen.
Auch ASME hat Standards für die Prüfung von Rohrleitungen entwickelt. Insbesondere ASME Sektion V für allgemeine zerstörungsfreie Prüfungen ist relevant für die Röntgenprüfung. Weiterhin sind Anforderung an das Bildformat und die Archivierung vorgegeben. So ist es oft gefordert das international anerkannte DICONDE Format zu wählen.
Diese Standards gewährleisten die Einhaltung von Industrierichtlinien und sorgen für zuverlässige und sichere Rohrleitungen in verschiedenen Anwendungen. Aufgrund der hohen Anforderungen an die Prüftechnik in diesem hochsensiblen Bereich ist es stark zu empfehlen einen fachkundigen Berater hinzuzuziehen.
Die Anforderungen von Unternehmen in der Öl und Gas Branche an die Qualitätskontrolle sind sehr unterschiedlich und lassen sich grob in verschiedene Kategorien einteilen. Für die Prüfung im laufenden Betrieb benötigen Unternehmen portable Systeme, mit denen im Feld auf Korrosion oder Verschleiß geprüft werden kann. Hier kommt es auf einen hohen Grad an Portabilität, Robustheit und Geschwindigkeit an.
Eine besondere Bedeutung kommt der Prüfung von Bauteilen am Ende des Herstellungsprozesses zu. Anbieter, die geringere Stückzahlen verarbeiten, benötigen manuelle Systeme für die Prüfung kleiner Chargen oder Einzelprüfungen. Hier ist die ECO H-Serie die perfekte Systemfamilie für kleinere Bauteile. Bei Bedarfen für die Prüfung für mittleren Volumen benötigen eine stärkere Automatisierung der 2D-Prüfung, CNC-Systeme und Chargenbeladung. Eine automatisierte Datenverarbeitung wird wichtiger. Im Falle von extrem hohen Volumen, zum Beispiel in der Serienprüfung im Automotive Bereich, sind hoch-performante Inlinesysteme mit automatischer Auswertung nötig. So können kürzeste Taktzeiten erreicht werden.
Ein weiterer Anwendungsfall ist die hochpräzise Computertomografie für messtechnische oder forensische Anwendung. Diese Messmaschinen müssen in einem klimatisierten Messraum untergebracht werden.
Die Auswahl des richtigen Systems kann komplex sein, und eine gute Entscheidung muss viele Parameter wie Größe, Geschwindigkeit, Kosten usw. abwägen. Kontaktieren Sie unsere Produktspezialisten für weitere Beratung.
Kontaktieren Sie uns noch heute
Verbessern Sie die Qualität und Sicherheit Ihrer Bauteile mit unseren hochmodernen Röntgensystemen und CT-Systemen. Kontaktieren Sie uns noch heute, um mehr über unsere Lösungen für die Materialprüfung zu erfahren. Unser Team steht Ihnen jederzeit gerne zur Verfügung, um Ihre Fragen zu beantworten und eine maßgeschneiderte Lösung für Ihre Anforderungen zu entwickeln.
Kontaktieren Sie unsere Experten, um über Ihre Projekte und Herausforderungen zu sprechen
Mit unseren Servicezentren und Hubs weltweit,
unterstützen wir Ihre Mitarbeiter mit maximaler
Effizienz in dem von Ihnen vorgegebenen Zeitrahmen und
ohne Ihren Betrieb zu unterbrechen.
Egal wo Sie sind, wir sind immer in Ihrer Nähe.
Unser Wissen und unsere Erfahrung
maximieren die Gewinne Ihres Unternehmens.