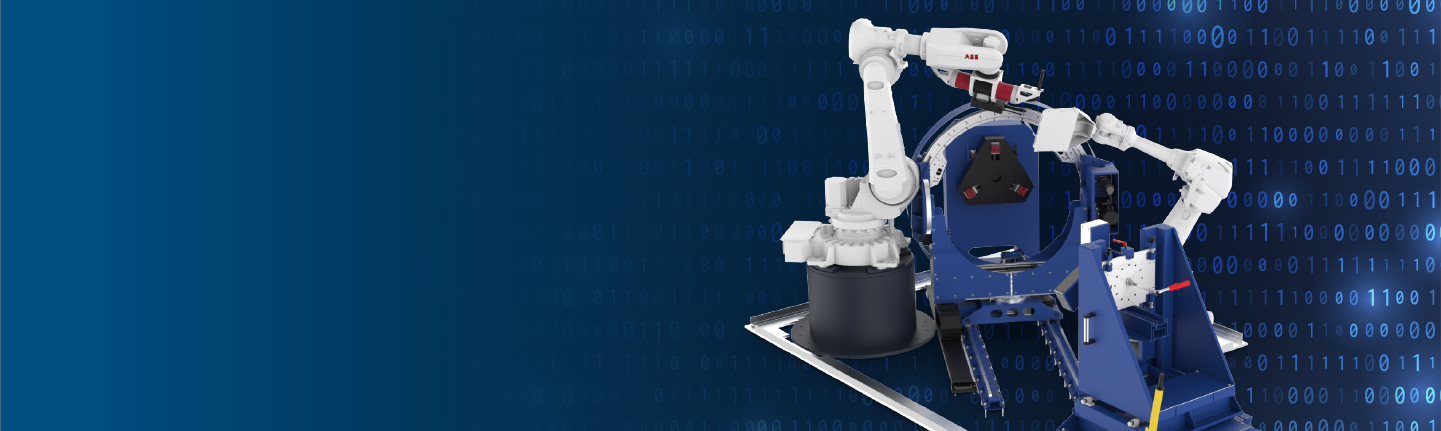
Automation in X-ray testing
Quality assurance (QA) automation is gaining relevance in various industries. This trend results from the drive for increased efficiency, consistency, and accuracy in testing processes. Automated testing enables better scalability and seamless integration into the production line. Automation can provide more comprehensive test coverage and improve application security. The use of machine learning and artificial intelligence enables the development of intelligent test systems. The trend is toward shift-left testing, where testing is integrated early in the development process. Here, computer tomography plays a major role in checking prototypes and pre-production series in detail. Overall, QA automation will continue to grow in importance to meet the increasing demands for manufacturing quality and efficiency.
Automating materials testing of components in QA presents several challenges. These include component diversity, automation adaptability, complex testing procedures, integration of sensors and measurement devices, defect detection, data acquisition, and management, cost and investment, compliance with standards and regulations, troubleshooting and maintenance, and the need for human interaction and expertise. Despite these challenges, automated materials testing systems offer many benefits for improved quality assurance. Despite these challenges, automated materials testing systems offer many benefits, including increased efficiency, accuracy, and consistency, resulting in overall improved quality assurance. By continuously advancing technologies and addressing specific requirements, many of these challenges can be successfully overcome.
Automated materials testing is often faster, less expensive, and with fewer risks for companies and people. VCxray has the highest level of expertise in standard and customized cabinet, conveyor, and robotic systems. VCxray designs and builds complete offline, at-line, and in-line inspection systems according to customer requirements.
With in-line inspection, the test parts are inspected directly and within the production flow. The inspection takes place continuously and automatically as long as production is running. The automated measurement data usually leads to automated decisions, so that in case of possible faults or defects, a production part is automatically sorted out and the corresponding data is reported back to the process. This integrated form of material inspection is particularly advantageous when high production throughput requires 100% inspection.
In other cases, the inspection remains on the production line. It allows materials inspectors to perform more complex measurement procedures so that test parts can be specially prepared, and even the simplest offline inspection systems can be made more efficient through automation, assisting inspectors with loading and manipulation and helping them make faster decisions.
ADR stands for "Automated Defect Recognition." In X-ray inspection, ADR refers to the automated analysis of X-ray images to detect defects, flaws or anomalies in components or materials.
X-ray inspection is an important method for non-destructive testing of components, especially in industry and quality assurance. By using X-rays, material defects such as cracks, voids, pores, foreign particles, and other irregularities inside components can be detected without having to damage the component.
Traditionally, X-ray images were manually interpreted by qualified inspectors or testing experts to identify potential defects. However, with advances in image processing technology and artificial intelligence, specialized algorithms and computer programs can be developed to automatically analyze X-ray images and identify defects.
The application of ADR in X-ray inspection offers several advantages, including:
Although ADR offers many benefits, it is important to note that there are also some challenges. The accuracy of the system depends on the quality of the training data, the algorithms used, and the ability of the system to detect different types of defects. Therefore, it is often necessary to train ADR systems with sufficient and representative data sets and validate them regularly to ensure that they provide reliable results.
AI (artificial intelligence) is increasingly being used for automatic defect recognition (ADR) in radiographs and has enabled significant advances in this area. Here are the basic steps on how AI can be used for automatic defect detection in X-ray images:
Using AI to automatically detect defects in X-ray images enables faster, more efficient, and more accurate quality control in various industries, such as automotive, aerospace, electronics manufacturing, and medical. However, it is important to emphasize that AI models cannot provide a definitive diagnosis and human expertise is still important to verify and validate results. However, AI can serve as a valuable tool to speed up the testing process and improve defect detection.
VCxray has an in-house developed AI toolbox for a wide variety of applications and a broad knowledge of how to use the technology in a standards-compliant manner. Contact us to learn how you can optimize your inspection processes using AI.
Automated X-ray inspection brings great efficiency gains - especially in production lines in industries with high production volumes of standard components. At the same time, process reliability and inspection consistency are increased by avoiding human error.
VCxray offers comprehensive tools for automatic image evaluation and defect detection (ADR). In many industries, it is necessary to achieve the fastest cycle times with absolute process reliability. Both can practically only be achieved by automating the X-ray inspection process. The VCxray toolbox is well known in many applications, especially in the automotive industry, and meets the standards of the industry and individual companies (BMW, VW, etc.). Here, one hundred percent X-ray inspection directly in production is mandatory. For more advanced inspections, such as completeness analyses, complex measurement tasks, density determinations, etc., VCxray has developed unique ADR and AI solutions that can be used to evaluate even the most complex metrics.
The ADR module can be integrated into all CNC-controlled systems at any time. For example, inspections in semi-automated booths can be fully automated. These can then be staffed with robots or even humans. If inline inspection with short cycle times is required, the solutions from the X-Line family are the ideal solution. The integration of barcode or RFID readers ensures the traceability of parts in the sense of Industry 4.0.
VCxray is regarded as the world's leading provider of highly complex automation systems for X-ray inspection and has created VAIP (VisiConsult Advanced Image Processing), a universal analysis tool, as well as AI implementations. This not only allows tasks such as defect detection or defect classification to be automated but also geometric measurements, component density, or completeness checks.
Inspection programs can be created or edited by trained operators without in-depth programming knowledge. In order not to disrupt production, this is done at special offline stations. A successful inspection concept naturally also includes data processing. The objects can be coded with RFID chips, barcodes, or number stamps. Internally, the inspection data is then stored in DICONDE servers, databases, or inspection reports. The system can also automate the direct marking of defect locations by stamping the inspection result. Two core tasks are the focus of any ADR system: maximum process reliability and maximum efficiency, with the goal of achieving these in a user-friendly environment.
Companies' requirements for quality control automation vary widely.
Depending on production volume and inspection standards, the use of automation, robotics, ADR, or AI is extremely economical and incidentally increases the quality of the inspection decision. This leads to less (pseudo) scrap and a better detection rate of critical defects.
In the case of extremely high volumes, for example in series production in the automotive sector, high-performance inline systems with automatic evaluation are often required. By means of robot loading or directly integrated into the production line, the shortest cycle times can be achieved. Cost-effectiveness must be evaluated with an ROI calculation.
Choosing the right system can be complex, and a good decision must weigh many parameters such as size, speed, cost, etc. Contact our product specialists for more advice.
Contact us today
Improve the quality and safety of your components with our state-of-the-art X-ray systems and CT systems. Contact us today to learn more about our material inspection solutions. Our team is always available to answer your questions and develop a customized solution for your needs.
Contact our experts to talk about your projects and challenges
With our Service centers and Hubs worldwide,
we will complete your staff with maximum
efficiency in your specified time frame and
without interrupting your operations.
No matter where you are, we are never far away.
Our knowledge and experience
maximize your company‘s profits.