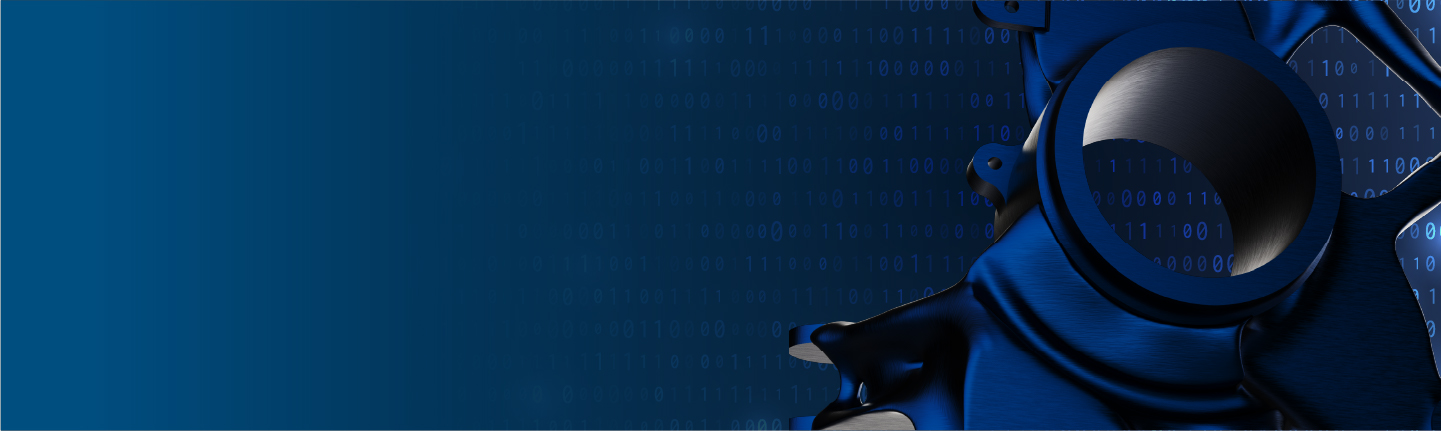
Computed Tomography
Computed tomography (CT) is an imaging technique used for non-destructive materials testing of components. It is based on conventional X-ray testing and in that sense represents an extension of two-dimensional testing. By visualizing the component in three dimensions, CT allows the detection of internal structures without physically destroying them.
The process of CT materials testing consists of several steps. First, the component to be inspected is rotated in the X-ray beam. The radiation penetrates the material and is absorbed to varying degrees by the different material densities and structures within the component. On the opposite side of the component is one or more detectors that measure the attenuated X-ray radiation. The detectors record the intensity of the radiation that has penetrated the component. As the component is rotated or moved through the CT scanner, a number of images, called projections, are taken. These data sets contain information about how the X-rays passed through the component. The many projections are processed with special algorithms to create a 3D reconstruction of the component. The software applies complex mathematical algorithms to visualize the internal structures. Analysis: The resulting 3D images allow a detailed examination of the internal structures of the component. Material defects such as cracks, voids, porosity, or inclusions can be detected, as well as internal geometries and defects.
CT materials inspection is used in various industries, including aerospace, automotive, mechanical engineering, electronics, and many others, where thorough and non-destructive inspection of components is critical.
Computed tomography (CT) offers a number of advantages in materials testing that make it an extremely powerful and valuable tool. Here are some of the key advantages of CT in materials testing:
One of the biggest advantages of CT is that it allows for non-destructive testing. This means that the material or component is not damaged or destroyed during the testing process. This is especially important if the component is needed for further testing or for actual use.
CT generates detailed 3D images that allow the internal structures of a material or component to be visualized. This allows complex internal geometries, defects, cracks, inclusions, voids and other material flaws to be identified and analyzed.
Modern CT scanners offer high resolution, which makes it possible to detect even the smallest details and defects in the material. As a result, even micro-cracks or other subtle irregularities can be revealed.
CT allows not only the visualization of internal structures, but also the accurate measurement and sizing of components and defects. This is especially valuable when precision and tolerance are critical.
CT can also be used for 3D metrology to determine the external and internal dimensions of a component. This is often difficult or impossible with conventional measurement techniques, especially when the internal geometry is complex.
CT also enables material analysis, including determination of material density, material composition and porosity. This allows important properties of the material to be assessed
CT can be applied to a variety of materials, including metals, plastics, ceramics, composites and more.
CT enables fast and efficient inspection of components, resulting in time and cost savings. The ability to immediately inspect the component for defects without disassembling it or performing extensive testing is a major advantage in industrial manufacturing and quality assurance.
Overall, computed tomography in materials testing provides a non-invasive, accurate and comprehensive method to evaluate the quality and integrity of materials and components to improve production processes and products.
The adoption of computed tomography (CT) for materials testing can present several challenges. These include the relatively high cost of purchasing and operating CT scanners, the complexity of the technology, the need for radiation protection measures, extensive data processing and analysis, and difficulties in handling large or heavy components. There is also the integration into existing processes and the potential impact on throughput to consider. Despite these challenges, the advantages of CT typically outweigh the disadvantages. Due to the high complexity of the inspection process, it is highly recommended to consult a specialist company for advice early and definitely before implementation. VCxray has a team of application specialists that can assist with implementation.
Computed tomography (CT) can perform a variety of measurement tasks in materials testing to evaluate the quality and integrity of materials and components. Some of the most important measurement tasks include:
CT is therefore a versatile tool in materials testing that enables comprehensive characterization and analysis of materials and components, facilitating quality testing and failure analysis in various industries.
The requirements for CT systems for non-destructive materials testing, metrology, and measurement vary widely due to the complex range of components and applications. Usually, extensive application studies are necessary to verify feasibility and conformity to standards before procurement.
VCxray has developed the QUICKscan process that allows users to obtain valuable results within minutes or even seconds. With this technology, CT inspections can be used for general quality control as they can also be performed "in line". Thanks to its modular design, CT can be added to almost any system at any time, including the ECO or PRO family of industrial systems, without the need to purchase an expensive new system. Switching between CT, manual testing, or even ADR can be done in seconds, providing unprecedented testing flexibility. When a highly accurate laboratory solution is needed, the diondo line is recommended. Built on a granite base, it is the perfect solution for the most demanding measurement tasks and laboratory applications.
Choosing the right system can therefore be complex, and a good decision must weigh many parameters such as size, speed, cost, etc. Contact our product specialists for further advice.
Contact us today
Improve the quality and safety of your components with our state-of-the-art X-ray systems and CT systems. Contact us today to learn more about our material inspection solutions. Our team is always available to answer your questions and develop a customized solution for your needs.
With our Service centers and Hubs worldwide,
we will complete your staff with maximum
efficiency in your specified time frame and
without interrupting your operations.
No matter where you are, we are never far away.
Our knowledge and experience
maximize your company‘s profits.