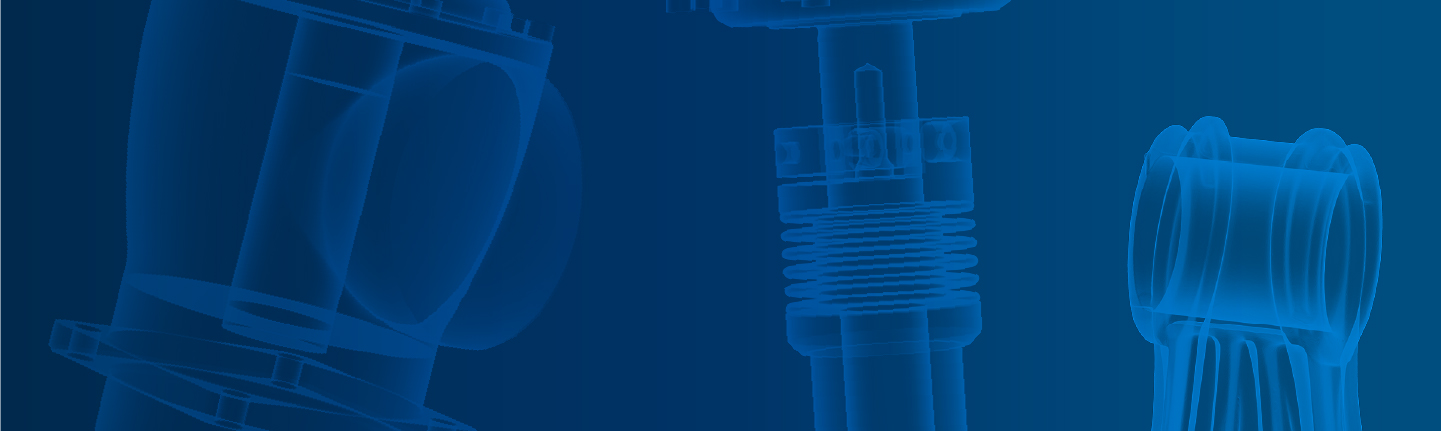
X-ray norms and standards
Norms and standards define uniform test procedures, test conditions and characteristic values. This ensures that materials from different manufacturers or sources can be tested under the same conditions. The results are thus comparable and enable engineers and scientists to evaluate materials objectively. By complying with norms and standards, manufacturers can ensure that their materials meet certain quality requirements. This is critical to producing products that meet expected performance and safety standards. Materials used in safety-critical applications must meet certain requirements to ensure the safety of people and the environment. Norms and standards establish these requirements and ensure that materials meet certain minimum standards. Many industries are subject to specific legal or regulatory requirements that affect the use of certain materials. Compliance with relevant norms and standards is often a prerequisite for meeting these requirements and obtaining approval for use in specific industries.
Overall, norms and standards play a critical role in materials testing by ensuring consistency, reliability, safety, and comparability, helping to promote high-quality and safe materials in a variety of applications.
In aerospace, there are several standards and norms for non-destructive testing (NDT) that must be followed to ensure the safety and quality of aircraft components. Here are some of the most important standards relevant to the aerospace industry:
Furthermore, there are a large number of standards and requirements that must be observed in aerospace. You can find a comprehensive overview in the NDT Toolbox App.
These standards have been developed by various organizations such as ASTM International, the European Committee for Standardization (CEN) and the National Aerospace and Defense Contractors Accreditation Program (NADCAP). They are internationally recognized and serve as a guide for conducting nondestructive materials testing in the aerospace industry. Compliance with these standards is critical to ensure the airworthiness and quality of aircraft components and to meet the high safety standards of the aerospace industry. As these standards are accompanied by high demands on the testing equipment, it is highly recommended to have the design of a testing system verified by a specialist company before implementation. VCxray has a team of application specialists that can assist with implementation.
International standards for X-ray inspection of piping include ISO 17636 for weld inspection, ISO 10893 for automated inspection of steel pipes, and EN 10246-7 for automated inspection of steel pipes. These standards specify requirements and procedures to ensure reliable and safe X-ray inspection. The choice of the appropriate standard depends on the specific requirements and application.
API has developed standards for X-ray inspection of piping, including API 1104 for welding, API 5L for line pipes, API 5CT for casing and tubing, and API 570 for in-service inspections.
ASME has also developed standards for piping inspection. In particular, ASME Section V for general non-destructive testing is relevant to X-ray inspection. Furthermore, image format requirements are specified. For example, the internationally recognized DICONDE format is often required.
There are many other standards for radiographic inspection of welds. The most widely used standard is ISO 17636-2, which is often cited by other standards. ASTM E 280 describes reference radiographs for fusion welds of steel. ASTM E 1416: Radioscopic inspection of welds.
These standards ensure compliance with industry guidelines and provide reliable and safe piping in various applications. Due to the stringent testing requirements in this highly sensitive area, it is strongly recommended that an expert consultant be consulted.
The ASTM E 2597 standard specifies the manufacturing characterization of digital detector arrays (DDAs). The purpose of the standard is to classify and assign quality numbers to DDAs for various applications and to perform various technical measurements.Basic requirements specified in the standards are efficiency, contrast sensitivity when using a step wedge, bad pixel calculations, image delay and burn-in, internal scatter, and resolution. A step wedge is required for calculating contrast sensitivity, material thickness range, and various thicknesses of prefilters. A two-wire IQI is used to measure the basic spatial resolution of the detector. The final results are recorded in a report and graphical analysis.
ASTM E 2737 describes the evaluation of digital detector array (DDA) systems and their long-term stability. It specifies various tests that must be performed at system acceptance and at specified intervals to track long-term stability The standard specifies tests for spatial resolution, geometric blur, scatter, signal-to-noise ratio, contrast sensitivity (contrast-to-noise ratio), image delay, and burn-in One of two usable phantoms should be used for these tests: The 5-slot wedge with various markings in the material. Duplex plate phantom with duplex wire IQI and hole IQI. In addition, software is needed to measure the above parameters. The VisiConsult Image Quality Evaluation Toolkit and the ASMT E 2737 Toolbox can be used for this purpose. The standard also describes how to handle calibration and bad pixels (which are additionally specified in ASTM E 2597) of the DDA system After completion of an inspection, all results must be documented in a data report that includes all inspection parameters and their time intervals.
All VCxray products comply with current norms and standards, and as a reputable we commit to continue to comply as standards evolve. Appropriate certifications are available for specific standards, please inquire for the appropriate standards for your application. Further, VCxray actively participates in the advancement of current standardization in bodies such as ISO and ASTM.
Contact our experts to talk about your projects and challenges
With our Service centers and Hubs worldwide,
we will complete your staff with maximum
efficiency in your specified time frame and
without interrupting your operations.
No matter where you are, we are never far away.
Our knowledge and experience
maximize your company‘s profits.